Plastic pelletizing plays a crucial role in the recycling process. In this step, the melt is converted into pellets. There are three different types of pelletizing:
- Hot die face pelletizing (HP)
- Strand pelletizing (SP)
- Underwater pelletizing (UWP)
The choice of pelletizing system depends on
- the material to be processed and
- the logistics conditions in production.
In this blog article we explain the various types of plastic pelletizing and their areas of application.
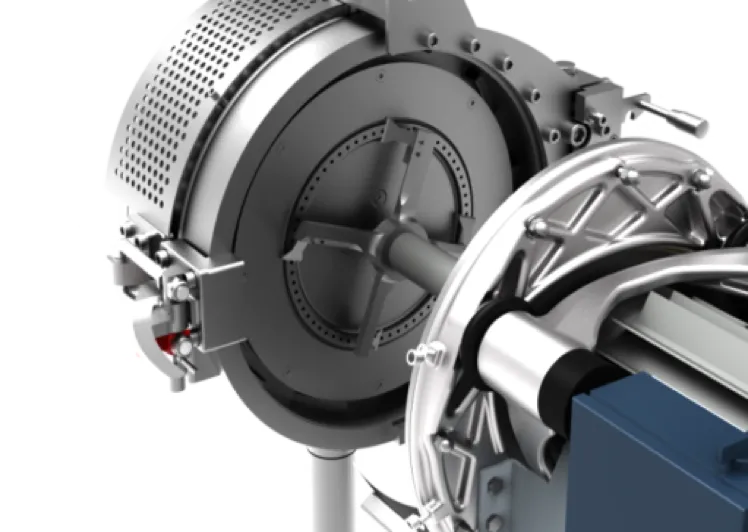
Hot die face pelletizing
Hot die face pelletizing involves the hot melt being cut by the knife (see also cold pelletizing). There are two types of hot die face pelletizing for processing plastics.
- Water ring hot die face pelletizing
- Air pelletizing
This form of pelletizing produces lenticular pellets.
Water ring hot die face pelletizing
This type of processing is used on many machines. It is particularly suitable for plastic pelletizing materials such as:
- Polyethylene (LDPE, LLDPE, HDPE)
- Polycarbonate
- Polystyrene
- Certain types of polyamide 6.0 with low MFI (Melt Flow Index)
How does water ring hot die face plastic pelletizing work?
- Transformation of melt into pellets
After filtration the plastic melt is fed to the die plate. It is pressed through the holes and converted into pellets by a cutting knife. The pressure that is used to press the melt through the die plate is decisive for a consistent shape and size of the pellet.
For this reason, some manufacturers, such as PURE LOOP, use sensors that measure the pressure behind the die plate. This makes it possible to adjust the blade speed for plastic pelletizing.
- Initial cooling by the water ring
When cutting the pellets, the knives reach up to 3,000 rpm. As a result, the material is ejected into the water ring. This is created by multiple nozzles, which produce a fine film of water around the inner wall of the chamber. In the water ring, the pellets are already undergoing initial cooling. This phase is an important step in plastic pelletizing. As a result of cooling, the material becomes hard on the outside and the heat is retained on the inside.
- Separating the pellets from the water in a pellet dewatering screen
The pellets and water are fed into a dewatering screen. In this basin, a shaker with a screen separates the pellets from the water. The water flows back into the basin through the screen holes. Meanwhile, the pellets are transported to the centrifuge for further processing.
The water in the basin must be replaced regularly and properly disposed of or treated. This maintenance work is important for high-quality plastic pelletizing. This is the only way to keep the system clean and prevent damage.
- Further drying with the centrifuge.
The centrifuge effectively separates the pellets from the remaining water. Depending on the manufacturer, the centrifuge can be aligned either vertically or horizontally:
- Vertical centrifuges often require a bearing or motor at the bottom. However, this results in higher maintenance costs, as water can penetrate these components. In addition, a fan is required to keep the material moving.
- Horizontal centrifuges dry the pellets as well as transport them to the final air-cooling line.
During this step, the pellets are still warm on the inside. This thermal energy helps to remove residual moisture during transport through the air-cooling line.
- Final cooling and drying in the cyclone
The pellets are then transported through a transport line into a cyclone (also known as a centrifuge). The final cooling and drying stage takes place inside this cyclone. After that, the pellets are ready for packaging. Some manufacturers also offer individual expansion options for color measurement or a weighing system. For specific adaptations as part of plastic pelletizing, talk to your manufacturer.
Air pelletizing
This type of plastic pelletizing is rarely used. It is primarily used for polyethylene. Air pelletizing works best when processing up to 150 kilograms per hour.
How does plastic pelletizing with air work?
- Transformation of melt into pellets
As with water ring hot die face pelletizing, the plastic melt is fed to the die plate after filtration. It is pressed through the holes, cut off with knives, and converted into pellets.
The pressure when pressing the melt through the die plate is decisive for the consistent shape and size of the pellets. Find out more about pressure during plastic pelletizing here.
- Cooling by air
The pellets are cut directly on the die plate with knives at up to 3,000 rpm. The speed of the blades propels the material into the air chamber. Here, initial cooling takes place through ventilation.
- Final cooling and drying in the cyclone
The fan transports the pellets through a transport line into a cyclone (centrifuge). Inside the cyclone, the material is finally cooled and dried before it is ready for packaging.
This last phase completes the plastic pelletizing process.
Strand pelletizing
Strand pelletizing is a form of cold pelletizing. This means that the melt is cooled down before it is cut into pellets (see also hot die face pelletizing). This method covers two types of plastic pelletizing:
- Conventional strand pelletizing
- Automatic strand pelletizing (ASP)
The pellets are cylindrical.
Conventional strand pelletizing
This method is suitable for plastics such as
- PET
- Polyamide
- Polypropylene
This form of plastic pelletizing is used less and less frequently due to its high space requirements and intensive operator involvement.
How does conventional strand pelletizing work?
- Transformation of the melt into strands
In the first step, the filtered melt is pressed through a melt strand head, which produces long plastic strands. These are also known colloquially as “spaghetti.”
An operator pulls these strands through a water basin, where they cool down. This direct and manual process highlights the extent of operator intervention required for this method of plastic pelletizing.
- Strand pelletizer
Cooling is followed by removing the water from the surface of the strands by drawing moisture away under suction.
Once the material is separated from the water, it enters the strand pelletizer. Here, two rollers cut the material with knives. During this step, the strands become pellets, which are used for further processing or as an end product.
- Drying and transporting the pellets
The plastic pellets are transported to the packaging area by an air blower or vibrating table. During transport, the material dries. However, with this type of pelletizing, most residual moisture remains in the pellet.
Automatic strand pelletizing
Automatic strand pelletizing (ASP) is a widely used method for plastic pelletizing.
How does automatic strand pelletizing (ASP) work?
- Transformation of the melt into strands
Following filtration, the plastic melt is formed into strands via a nozzle. These are then immediately placed on a slide, which is continuously drizzled with water to cool the material.
At the end of the slide, the water is separated from the strands.
- Plastic pelletizing
The material, which is still slightly moist, is converted into pellets by knives. They are then fed into a shaker basin to remove residual moisture. Here, the shaker uses a screen to separate the pellets from the remaining water.
- Drying in the centrifuge
The centrifuge is responsible for further drying during the plastic pelletizing process. Depending on the manufacturer, the centrifuge is aligned either vertically or horizontally.
- Final drying in the cyclone
Next, the pellets are fed through a transport line into a cyclone (centrifuge). Inside, it undergoes final cooling and drying before it is ready for packaging.
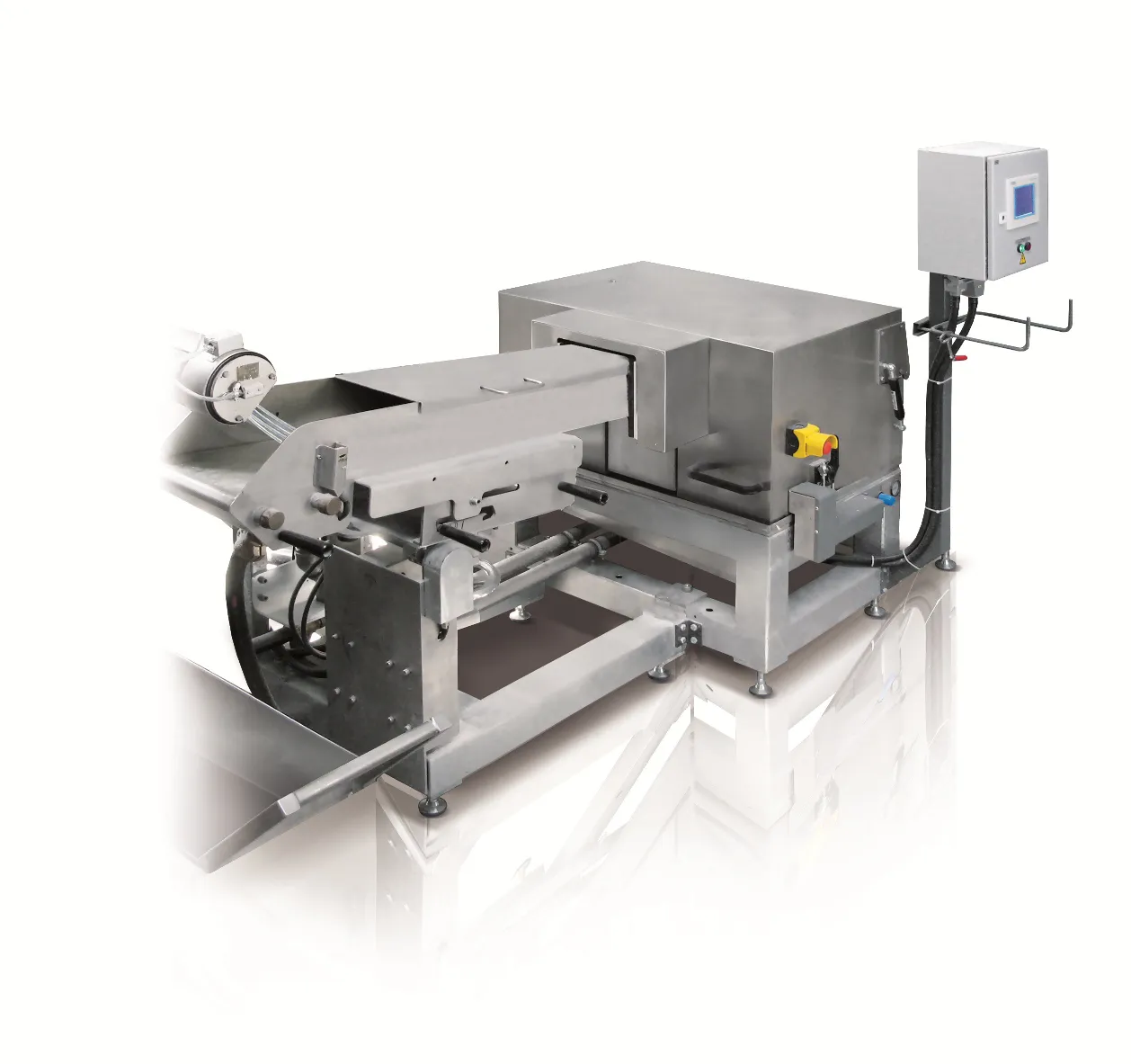
Underwater pelletizing (UWP)
This method of plastic pelletizing is a combination of hot die face pelletizing and strand pelletizing.
They can be used for any polymer. This is possible because of the flexibility of the system. UWP can be used very cold, but also very hot. It can also be carried out in air instead of water.
High-priced underwater pelletizing is a true all-rounder for plastic pelletizing. The result is spherical pellets.
How does UWP work?
- Starting up the machine and adjusting the melt diverter
When starting up the system, it is crucial to set the melt diverter correctly. This prevents premature overfilling of the pelletizing system with the material. The melt is fed into a basin below to avoid overloading the system.
At the same time, the cutting chamber is filled with water. As soon as the machine is ready, the melt diverter is switched over and the plastic pelletizing process begins.
- Transformation of melt into pellets
During pelletizing, the melt is pressed through a die plate and cut directly by a knife. The cutting chamber, which is filled with water, ensures immediate and effective cooling of the material.
- Continuous cooling along the transport line
The material is then transported in water along a line to the centrifuge. The cooling process continues while the material is being transported.
Just before the centrifuge, there is a separation chamber. Inside it, the pellets are separated from the water. The excess water flows into a basin underneath.
- Final drying in the centrifuge
After final drying in the centrifuge, the pellets are ready for packaging. The carefully coordinated process used during the UWP method guarantees a high-quality end product from plastic pelletizing.
The various types of plastic pelletizing at a glance.
Plastic pelletizing is not only a crucial step in the recycling process, but also an area of continuous technological progress. By assessing the three main methods in detail
- hot die face pelletizing,
- strand pelletizing, and
- underwater pelletizing
— it becomes clear how diverse the options for processing a wide variety of types of plastic are. Each method offers specific advantages that make it ideal for specific applications and materials.
System |
Abbreviation |
Advantages |
Disadvantages |
Pellet shape |
Application |
Hot die face pelletizing |
HP |
Direct conversion of melt to pellets; high efficiency |
Materials with a high MFI (melt flow index) cannot be processed. |
Lenticular |
Polyethylene, polycarbonate, polystyrene, polypropylene, polyamide with low MFI |
Strand pelletizing |
SP |
Good pellet size control; simple technology |
Space-intensive; operator-intensive, high dust content with brittle materials. |
Cylindrical |
PET, polyamide, polypropylene |
Underwater pelletizing |
UWP |
High flexibility; uniform pellet size; efficient cooling |
Higher purchase and maintenance costs |
Spherical |
Wide range of polymers |
The choice of pelletizing system depends largely on the material requirements and logistics situation on site. Each process has its place and plays an important role in the overall context of plastic pelletizing.