Die Granulierung von Kunststoffen spielt eine entscheidende Rolle im Recyclingprozess. Bei diesem Schritt wird die Schmelze zu Granulat umgeformt. Es gibt drei unterschiedliche Typen der Granulierung:
- Heißabschlag-Granulierung (HG)
- Stranggranulierung (SP)
- Unterwassergranulierung (UWG)
Die Wahl des Granuliersystems ist abhängig vom
- zu verarbeitenden Material und
- der logistischen Gegebenheiten in der Produktion.
In diesem Blogartikel beleuchten wir die verschiedenen Typen der Kunststoff-Granulierung und deren Anwendungsgebiete.
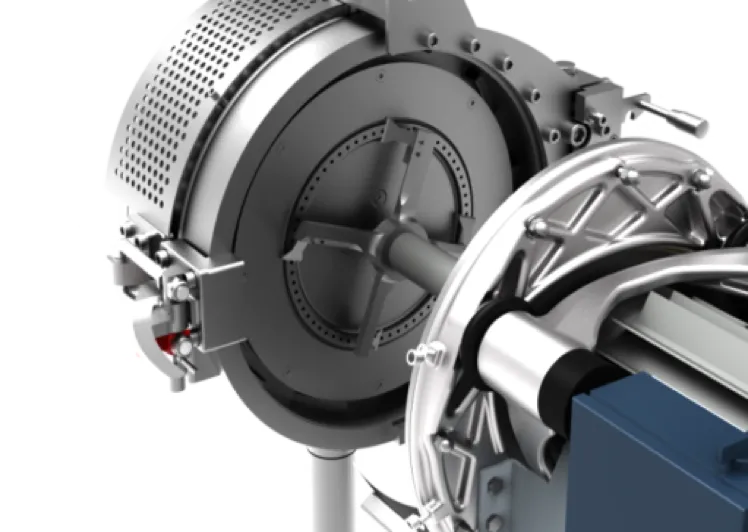
Heißabschlag-Granulierung
Heißabschlag bedeutet, dass die warme beziehungsweise heiße Schmelze vom Messer geschnitten wird (siehe auch Kaltabschlag). Es gibt zwei Arten von Heißabschlag-Granulierung zur Verarbeitung von Kunststoffen.
- Wasserring-Heißabschlag-Granulierung
- Luftgranulierung
Bei dieser Form der Granulierung entstehen linsenförmige Pellets.
Wasserring-Heißabschlag-Granulierung
Diese Art der Verarbeitung kommt auf vielen Maschinen zum Einsatz. Sie eignet sich vor allem für die Granulierung von Kunststoffen:
- Polyethylen (LDPE, LLDPE, HDPE)
- Polycarbonat
- Polystyrol
- Bestimmte Arten von Polyamid 6.0 mit niedrigem MFI (Melt Flow Index)
Wie funktioniert die Wasserring-Heißabschlag-Granulierung von Kunststoffen?
- Umwandlung der Schmelze in Granulat
Nach der Filtration wird die Kunststoffschmelze zur Lochplatte geführt. Hier wird sie durch die Löcher gepresst und mit einem Schneidemesser in Granulat umgewandelt. Für eine konsistente Form und Größe ist der Druck, mit dem die Schmelze durch die Lochplatte gepresst wird, entscheidend.
Aus diesem Grund setzen einige Hersteller wie PURE LOOP Sensoren ein, die den Druck hinter der Lochplatte messen. Dies ermöglicht eine Anpassung der Messergeschwindigkeit im Rahmen der Kunststoff-Granulierung.
- Initiale Kühlung durch den Wasserring
Beim Schneiden des Granulats erreichen die Messer bis zu 3.000 Umdrehungen pro Minute. Dadurch wird das Material in den Wasserring geschleudert. Dieser entsteht durch mehrere Düsen, die einen feinen Wasserfilm entlang der Innenwand der Kammer erzeugen.
Im Wasserring erfährt das Granulat bereits eine erste Abkühlung. Diese Phase ist ein wichtiger Schritt in der Granulierung von Kunststoffen. Durch die Kühlung wird das Material außen bereits hart und innen bleibt die Wärme erhalten.
- Trennen von Granulat und Wasser im Granulat-Entwässerungssieb
Das Granulat wird zusammen mit dem Wasser in ein Entwässerungssieb geleitet. In diesem Becken sorgt eine Schüttelrinne mit einem Sieb für die Trennung des Granulats vom Wasser. Das Wasser fließt durch die Sieblöcher zurück ins Becken. Währenddessen wird das Granulat zur weiteren Verarbeitung in die Zentrifuge transportiert.
Das Wasser im Becken muss regelmäßig ersetzet und fachgerecht entsorgt oder aufbereitet werden. Für eine qualitative Kunststoff-Granulierung ist diese Wartungsarbeit wichtig. Nur so bleibt die Anlage sauber und Schäden werden verhindert.
- Die Zentrifuge zur weiteren Trocknung
Die Zentrifuge trennt das Granulat effektiv vom restlichen Wasser. Abhängig vom Hersteller kann die Zentrifuge entweder vertikal oder horizontal ausgerichtet sein:
- Vertikale Zentrifugen benötigen oft ein Lager oder einen Motor im unteren Bereich. Das führt jedoch zu einem höheren Wartungsaufwand, da Wasser in diese Komponenten eindringen kann. Zusätzlich ist ein Gebläse erforderlich, um das Material anschließend weiterzubewegen.
- Horizontale Zentrifugen übernehmen sowohl die Trocknung des Granulats als auch den Weitertransport zur abschließenden Luftkühlstrecke.
Bei diesem Schritt ist das Granulat nach wie vor im Inneren noch warm. Diese Wärme hilft beim Transport über die Luftkühlstrecke die Restfeuchte zu entfernen.
- Abschlusskühlung und -trocknung im Zyklon
Anschließend wird das Granulat durch eine Transportleitung in einen Zyklon (auch Fliehkraftabscheider genannt) befördert. Innerhalb dieses Zyklons kommt es zur finalen Abkühlung und Trocknung. Danach ist es zur Abfüllung bereit. Manche Hersteller bieten zusätzlich individuelle Erweiterungsoptionen zur Farbmessung oder eine Waage. Für spezifische Anpassungen im Rahmen der Granulierung von Kunststoffen sprechen Sie mit dem Hersteller Ihres Vertrauens.
Luftgranulierung
Diese Art der Kunststoff-Granulierung findet selten Verwendung. Sie kommt vor allem bei Polyethylen zum Einsatz. Luftgranulierung funktioniert optimal bei der Verarbeitung von bis zu 150 Kilo pro Stunde.
Wie funktioniert die Granulierung von Kunststoffen mit Luft?
- Umwandlung der Schmelze in Granulat
Wie bei der Wasserring-Heißabschlag-Granulierung wird die Kunststoffschmelze nach der Filtration zur Lochplatte geführt. Dort wird sie durch die Löcher gepresst, mit Messern abgeschnitten und so in Granulat umgewandelt.
Für die gleichbleibende Form und Größe ist der Druck beim Durchpressen der Schmelze durch die Lochplatte entscheidend. Genaueres zum Druck während des Granulierung von Kunststoffen entdecken Sie hier.
- Kühlung durch Luft
Direkt an der Lochplatte wird das Granulat mit Messern mit bis zu 3.000 Umdrehungen pro Minute geschnitten. Durch die Geschwindigkeit der Messer wird das Material in die Luftkammer befördert. Hier erfolgt eine erste Abkühlung durch eine Belüftung.
- Finale Kühlung und Trocknung im Zyklon
Das Gebläse transportiert das Granulat durch eine Transportleitung in einen Zyklon (Fliehkraftabscheider). Innerhalb des Zyklons erfolgen die abschließende Kühlung und Trocknung des Materials, bevor es bereit für die Abfüllung ist.
Diese letzte Phase schließt den Prozess der Kunststoff-Granulierung ab.
Stranggranulierung
Die Stranggranulierung ist eine Form der Kaltabschlaggranulierung. Das bedeutet, dass die Schmelze vor dem Schneiden zum Granulat abgekühlt wird (siehe auch Heißabschlag). Diese Methode umfasst zwei Arten der Granulierung von Kunststoffen:
- Klassische Stranggranulierung
- Automatische Stranggranulierung (ASP)
Das Granulat ist zylinderförmig.
Klassische Stranggranulierung
Für diese Methode eignen sich Kunststoffe wie
- PET
- Polyamid
- Polypropylen
Diese Form der Granulierung von Kunststoffen wird aufgrund ihres hohen Platzbedarfs und der intensiven Bedienerführung zunehmend seltener angewandt.
Wie funktioniert die klassische Stranggranulierung?
- Umwandlung der Schmelze in Stränge
Im ersten Schritt wird die gefilterte Schmelze durch einen Schmelzestrangkopf gepresst, wodurch lange Kunststoffstränge entstehen. Diese werden umgangssprachlich auch „Spaghetti“ genannt.
Ein Bediener zieht diese Stränge durch ein Wasserbecken, wo sie abkühlen. Dieser direkte und manuelle Prozess unterstreicht die Bedienerintensität dieser Methode innerhalb der Granulierung von Kunststoffen.
- Stranggranulator
Nach der Abkühlung folgt die Entfernung des Wassers von der Oberfläche der Stränge durch die Strangabsaugung.
Ist das Material vom Wasser getrennt, gelangt es in den Stranggranulator. Hier zerschneiden zwei Walzen mit Messern das Material. Durch diesen Schritt wird aus den Strängen das Granulat, das zur weiteren Verarbeitung oder als Endprodukt dient.
- Trocknung und Transport des Granulats
Anschließend wird das Kunststoff-Granulat über ein Luftgebläse oder einen Rütteltisch weiterbefördert in Richtung Abfüllung. Währenddessen trocknet das Material. Jedoch bleibt bei dieser Art der Granulierung am meisten Restfeuchte im Granulat.
Automatische Stranggranulierung
Eine weit verbreitete Methode zur Granulierung von Kunststoffen ist die automatische Stranggranulierung (ASP).
Wie funktioniert die automatische Stranggranulierung (ASP)?
- Umwandlung der Schmelze in Stränge
Nach der Filtrierung wird die Kunststoffschmelze über eine Düse in Stränge geformt. Diese gelangen anschließend sofort auf eine Rutsche, die kontinuierlich mit Wasser beträufelt wird, um das Material abzukühlen.
Am Ende der Rutsche findet die Separierung des Wassers von den Strängen statt.
- Kunststoff-Granulierung
Das noch leicht feuchte Material wird durch Messer in Granulat umgewandelt. Um die Restfeuchte zu entfernen, folgt ein Schüttelbecken. Hier trennt die Schüttelrinne mit einem Sieb das Granulat vom verbleibenden Wasser.
- Trocknung mittels Zentrifuge
Die Zentrifuge ist für die weitere Trocknung während der Granulierung von Kunststoffen verantwortlich. Je nach Hersteller ist die Zentrifuge vertikal oder horizontal ausgerichtet.
- Finale Trocknung im Zyklon
Abschließend wird das Granulat durch eine Transportleitung in einen Zyklon (Fliehkraftabscheider) geleitet. Dort erfährt es eine abschließende Abkühlung und Trocknung, bevor es für die Abfüllung bereit ist.
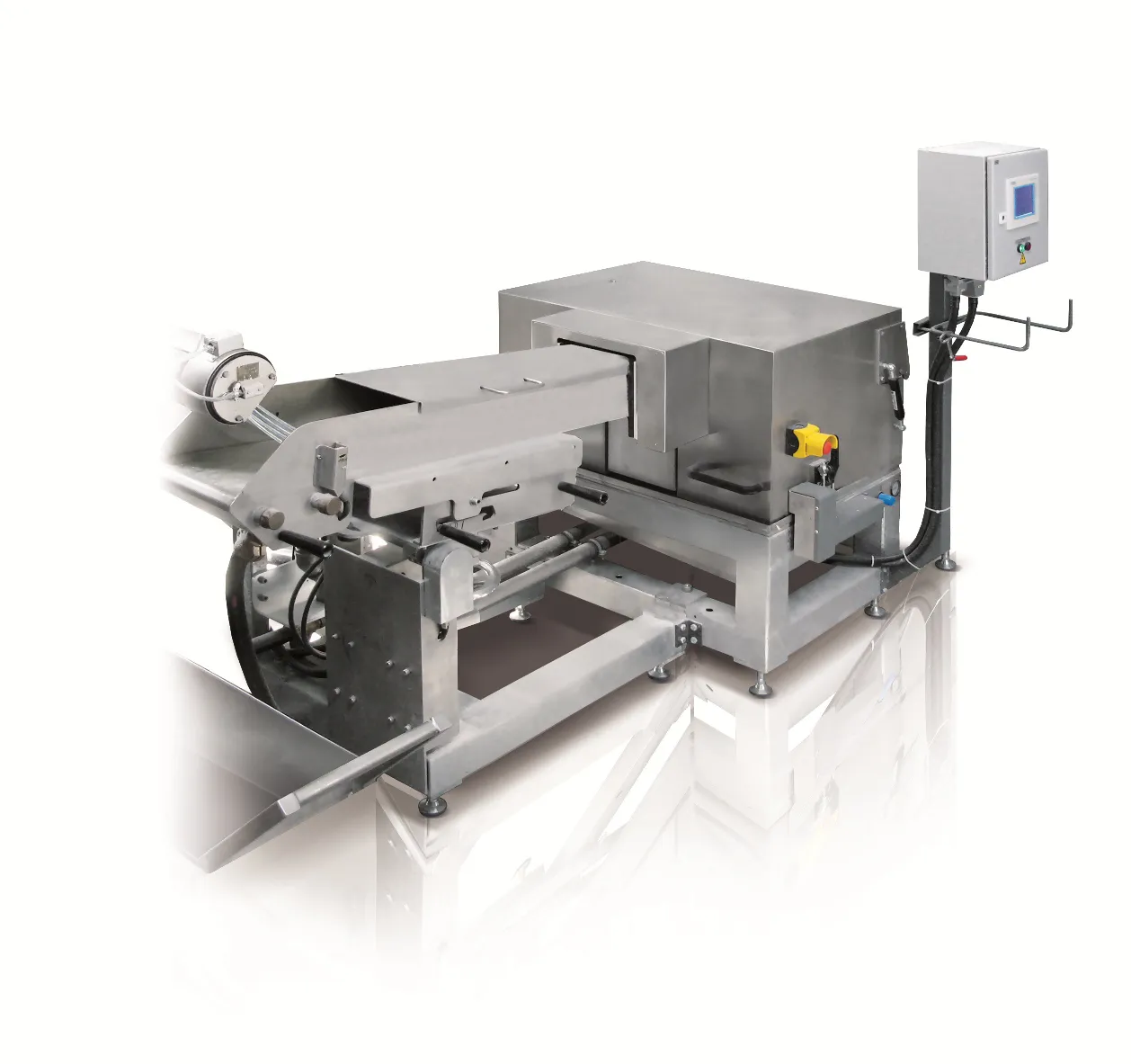
Unterwassergranulierung (UWG)
Diese Weise der Kunststoff-Granulierung ist eine Kombination aus Heißabschlag- und Stranggranulierung.
Sie bei jedem Polymer angewendet werden. Ermöglicht wird das durch die Flexibilität der Anlage. Die UWG kann sehr kalt, aber auch sehr heiß gefahren werden. Ebenso kann sie mit Luft statt mit Wasser betrieben werden.
Die hochpreisige Unterwassergranulierung ist ein wahrer Allrounder zur Granulierung von Kunststoffen. Das Endergebnis ist kugelförmiges Granulat.
Wie funktioniert die UWG?
- Anlagenstart und einstellen der Schmelzweiche
Beim Anfahren der Anlage ist es entscheidend, die Schmelzweiche korrekt einzustellen. Dies verhindert eine vorzeitige Überfüllung des Granuliersystems mit Material. Die Schmelze wird in eine darunterliegende Wanne geleitet, um eine Überlastung zu vermeiden.
Parallel dazu befüllt sich die Schneidkammer mit Wasser. Sobald die Maschine bereit ist, wird die Schmelzweiche umgestellt und die Granulierung der Kunststoffe beginnt.
- Umwandlung der Schmelze in Granulat
Zur Granulierung wird die Schmelze durch eine Lochplatte gepresst und unmittelbar von einem Messer geschnitten. Die vollständig mit Wasser gefüllte Schneidkammer sorgt für eine sofortige und effektive Abkühlung des Materials.
- Kontinuierliche Kühlung entlang der Förderstrecke
Anschließend wird das Material entlang einer Förderstrecke im Wasser zur Zentrifuge transportiert. Auf diesem Weg wird der Kühlprozess fortgesetzt.
Kurz vor der Zentrifuge ist eine Separationskammer. Hier wird das Granulat vom Wasser getrennt. Das überschüssige Wasser fließt dabei in ein untergeordnetes Becken.
- Abschließende Trocknung in der Zentrifuge
Nach der finalen Trocknung in der Zentrifuge ist es bereit für die Abfüllung. Die UWG-Methode garantiert durch diesen sorgfältig abgestimmten Prozess ein hochwertiges Endprodukt in der Granulierung von Kunststoffen.
Die verschiedenen Arten der Granulierung von Kunststoffen auf einen Blick
Die Kunststoff-Granulierung ist nicht nur ein entscheidender Schritt im Recyclingprozess, sondern auch ein Bereich stetiger technologischer Fortschritte. Durch die detaillierte Betrachtung der drei Hauptmethoden
- Heißabschlag-Granulierung,
- Stranggranulierung und
- Unterwassergranulierung
– wird deutlich, wie vielfältig die Möglichkeiten zur Verarbeitung verschiedenster Kunststofftypen sind. Jede Methode bietet spezifische Vorteile, die sie für bestimmte Anwendungen und Materialien prädestinieren.
System |
Abkürzung |
Vorteile |
Nachteile |
Granulatform |
Anwendung |
Heißabschlag-Granulierung |
HG |
Direkte Umwandlung von Schmelze zu Granulat; hohe Effizienz |
Materialien mit hohem MFI (melt flow index) sind nicht verarbeitbar. |
linsenförmig |
Polyethylen, Polycarbonat, Polystyrol, Polypropylen Polyamid mit niedrigem MFI |
Strang-granulierung |
SP |
Gute Kontrolle über die Granulatgröße; einfache Technologie |
Platzintensiv; bedienerintensiv, hoher Anteil an Staub bei spröden Materialien. |
zylinderförmig |
PET, Polyamid, Polypropylen |
Unterwasser-granulierung |
UWG |
Hohe Flexibilität; gleichmäßige Granulatgröße; effiziente Kühlung |
Höhere Anschaffungs- und Wartungskosten |
kugelförmig |
Breites Spektrum an Polymeren |
Die Wahl des Granuliersystems hängt stark von den Anforderungen des Materials und den logistischen Gegebenheiten ab. Jedes Verfahren hat seine Daseinsberechtigung und spielt eine wichtige Rolle im Gesamtkontext der Granulierung von Kunststoffen.